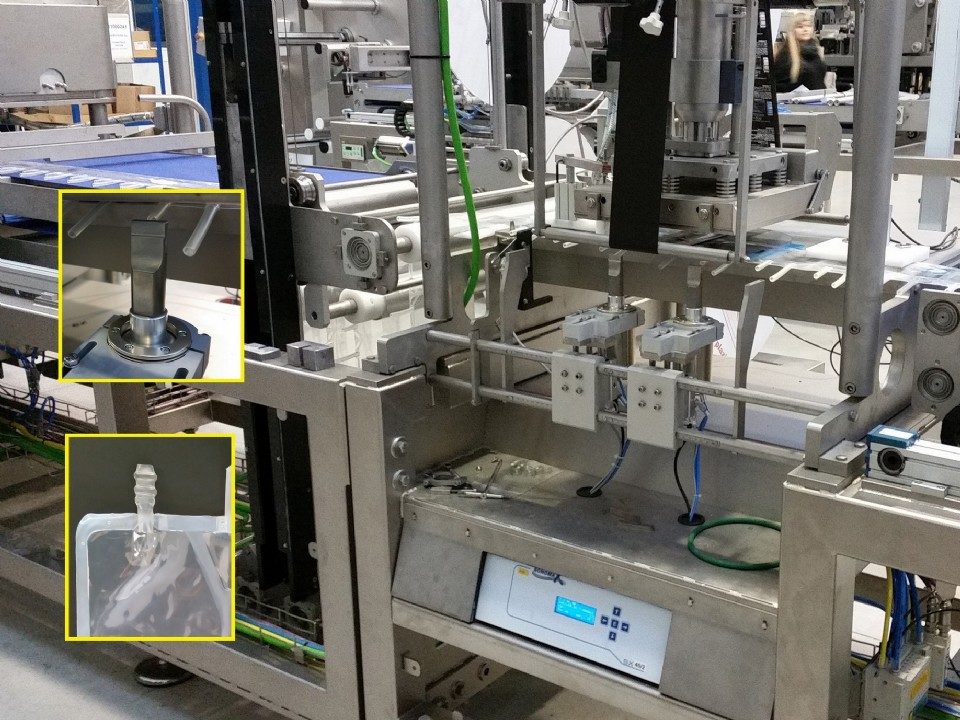
Health and safety
We are familiar with the medical sector and its requirements.
From clean room to surgical use, medical devices demand the highest standards of safety, airtightness and hygiene.
That is why we offer you advice at all stages of processing: to ensure process stability and reproducibility.
Furthermore, with our ultrasonic systems you can monitor all welding parameters through software, eliminating errors, deviations and problems of any kind.
Key Advantages of Ultrasonic Welding for Medical Applications
- Accuracy and Reliability
Ultrasonic welding offers high precision in joining components, ensuring that welds are strong and reliable. This is critical in medical equipment, where the integrity of joints can directly affect safety and performance.
- Sterility and Cleanliness
The process requires no adhesives or solvents, minimising the risk of contamination. This is crucial in medical applications, such as the production of surgical instruments and implants.
- Speed and Efficiency
Ultrasonic welding is remarkably fast, often completing welds in less than a second. This fast cycle time increases productivity, enabling manufacturers to produce a high volume of medical devices efficiently.
- Energy Efficiency
The technique requires less energy than conventional welding methods, as it generates heat only at the joint interface. This not only reduces operating costs, but also supports environmentally friendly production practices.
- Minimal Thermal Impact
Since ultrasonic welding applies heat selectively and for a very short duration, there is minimal thermal damage to components. This is especially important for sensitive materials used in medical devices, preserving their integrity and functionality.
- Versatility with Materials
Ultrasonic welding can join a wide range of thermoplastic materials, including rigid and flexible components. This versatility enables innovative designs and material combinations in medical devices.
- Automated Process Control
The technology can be easily automated, enabling consistent quality control during production. Automated systems can monitor parameters to ensure that optimal welding conditions are maintained, vital for critical medical applications.
- Economic Convenience
By eliminating the need for additional joining materials such as adhesives or fasteners, ultrasonic welding reduces material costs and simplifies the production process, contributing to overall savings.
- Robust Junction Integrity
Fusion at the molecular level achieved through ultrasonic welding results in joints that show comparable strength to base materials. This ensures that medical devices can withstand mechanical stress during use.
- No Mechanical Weak Points
Unlike traditional methods that can introduce mechanical weaknesses due to fasteners or adhesives, ultrasonic welding creates seamless joints that improve the durability of medical products.
These advantages make ultrasonic welding an optimal choice for various applications in the medical field, from manufacturing complex devices to ensuring the safety and efficacy of critical medical products.
Automatic plant for production of surgical masks T-Mask 2 produced by Texma Srl
You can weld
- Surgical masks
- Blood containers and filters
- Medical filters
- Phlebo
- TNT aprons and coats
- Fluid bags
- Syringes / butterfly
- Hospital drapes
Advantages
- Reliability
- Extreme functionality
- Process monitoring
- Highest quality
- Research and development